We all wonder if the day will come when robots become almost like characters out of a sci-fi novel — intelligent, intuitive, and surprisingly human in their interactions. Welcome to the era of Industry 4.0 technologies, where robots and humans collaborate to dramatically improve efficiency and safety in industrial environments. In this world, technology isn’t just a bunch of devices and code; it's an intelligent, integral part of our industrial fabric.
Here’s something to ponder: By 2025, the value creation potential of Industry 4.0 for manufacturers and suppliers is expected to skyrocket to an eye-popping $3.7 trillion. That's not just a number; it's a whole universe of opportunities, innovations, and breakthroughs in efficiency in the otherwise straightforward industrial world.
Get Our eBook
Learn about Industry 4.0 technology
Download PDF
But what are these Industry 4.0 technologies, and how is the vision of manufacturing automation becoming a reality? Dive into our guide, and you’ll find yourself on a journey through the exciting landscape of Industry 4.0. We're talking about AI that's more of a creative collaborator than a robot and IoT devices that don’t just process data but tell stories of efficiency and ingenuity in real time.
So, grab a cup of your favorite beverage, and let’s embark on this adventure together. We will explore the nooks and crannies of Industry 4.0 technologies, uncovering insights and tips that are not just about keeping pace with change but embracing and leading it. The journey into the heart of this new era is both thrilling and profoundly transformative.
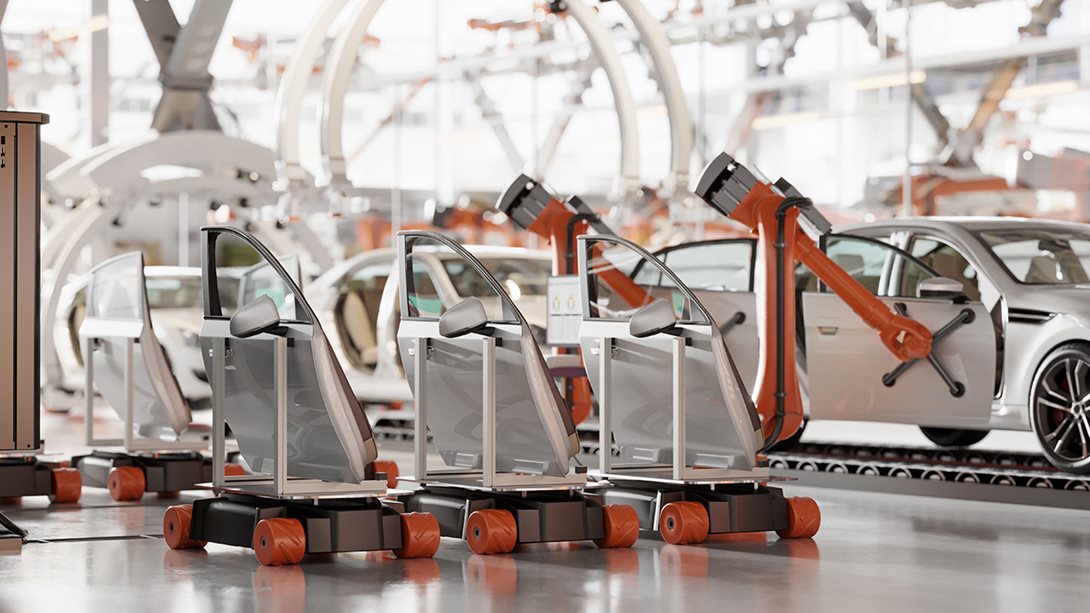
The Core Technologies of Industry 4.0
Imagine stepping into a world where technology doesn't just function behind the scenes; it communicates, adapts, and even thinks and learns alongside us. Welcome to the vivid landscape of the Fourth Industrial Revolution or 4IR — a place where each technology is not just a tool but a partner in our industrial narrative.
1. Fast Networks — The Warriors of Speed
With 4G LTE being nearly ubiquitous today, the 5G rollout is in full swing, and 6G on the horizon, we now have the uplink and downlink speeds required for real-time data throughput required for edge computing. This means latency can be reduced to near zero across vast industrial spaces, enabling automation, predictive maintenance and highly efficient operations.
2. Optimized Devices — The Maestros of Precision
Smart devices are the maestros of efficient industrial operations, with built-in intelligence and edge computing capabilities that enable critical processes — formerly handled by servers in remote data centers — to occur wherever the devices are deployed. In the hands of a device like Digi IX40, industrial automation can occur with accuracy and efficiency, leading to enormous ROI.
3. Advanced Camera Systems — The Observant Eyes
More than just visual devices, smart camera and video systems are the eyes of the industrial automation landscape. Built with integrated sensors and processors, they can take full advantage of the edge computing paradigm, perform computations and deliver mission-critical data. In a practical example, this could include everything from alerts about defects to launching a process to shut down operations to prevent catastrophic errors. Before the human eye could detect an anomaly, smart cameras can detect an issue, halt a process, or launch a service ticket in advance of a breakdown.
4. Real-Time Processing — The Supersonic Jet Engine
In the blink of an eye, real-time processing enables precise operations on production lines, instantaneous communications from machine to machine, and rapid, actionable insights for operators. Faster processing at the edge enables increased output, faster detection of anomalies in production lines, and industrial automation capabilities. Sensors and edge computing systems create vast amounts of data; real-time processing at the edge of the network enables these systems to process data immediately and relay only the critical actionable data to a central platform for human operators to analyze.
5. Robotics — The Tireless Workers
Robots can perform tirelessly on factory floors, efficiently performing tasks without fatigue. Whereas human workers need breaks, can only work so quickly, and can easily make mistakes, robots can work 24/7 without error and can even report when they need servicing. Today, "cobots" — or collaborative robots — work alongside human workers for the optimal blend of human intelligence and machine efficiency.
6. AI and Machine Learning — The Data Magicians
AI and ML can transform cold data into visions of what could be. They're not just crunching numbers; they're foreseeing challenges, learning and improving upon processes faster than is possible for the human brain, and developing solutions that redefine what we thought possible. As a simple example, when a defect is detected in an assembly line, an AI-driven system can learn what that looks like, what led to the defect, and identify its cause much faster the next time. This is one of the key concepts in predictive maintenance.
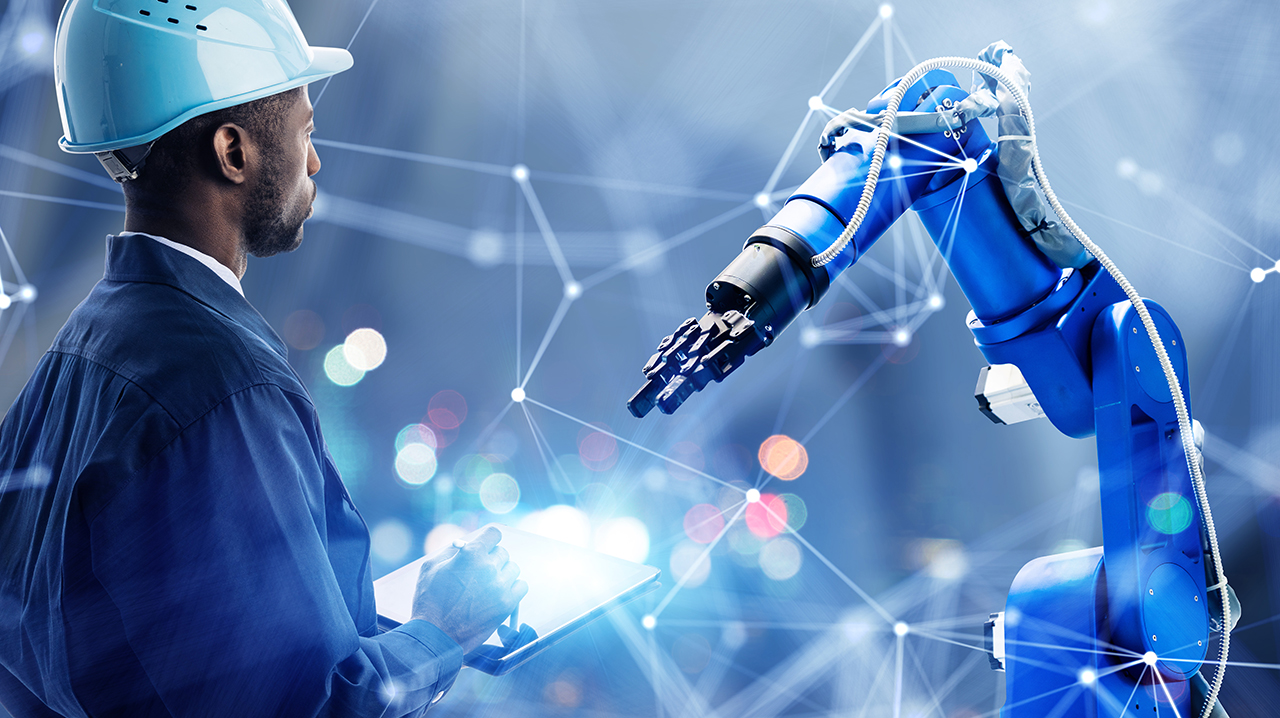
The Role of Edge Computing in Industry 4.0
Edge computing plays an integral role in the Industry 4.0 ecosystem. It enables real-time data processing by bringing computation closer to data sources. Moreover, it complements other Industry 4.0 technologies by reducing latency and improving response times in smart manufacturing environments. Robotics, process control, predictive maintenance and rapid response to critical issues on the manufacturing floor are all dependent on the rapid processing capabilities of edge computing.
Get Our Solution Brief
Learn how edge computing solves networking challenges
Download PDF
Tips for Implementing Industry 4.0 Technologies
1. Proper training and skills acquisition for staff
In the transformative world of Industry 4.0, equipping your team with the right knowledge is paramount. The intricacies of these technologies define success in this era. Employees need to be trained effectively to harness their full potential.
Linda Shaffer, Chief People Operations Officer at Checkr, says, "It's not just about having the best tech. The human element, your team, plays a pivotal role. Employees equipped with the right training principles can make data-driven decisions, optimize processes, and enhance system reliability."
However, the journey to competency starts with recognizing that these technologies, though promising, bring new intricacies. These can range from data management protocols to security concerns. Staffing developers with the expertise to navigate these nuances is crucial.
Beyond making staffing decisions, investing in continuous training and workshops can't be emphasized enough, as the industrial IoT is dynamic and continually advancing.
2. Ensuring compatibility with other Industry 4.0 technologies
Tip 1: Prioritize open standards
Jim Pendergast, Senior Vice President at altLINE Sobanco, emphasizes the importance of open standards. "Open standards are key in fostering interoperability, allowing diverse Industry 4.0 technologies, from IoT sensors to AI algorithms, to communicate effortlessly."
Tip 2: Regularly update and patch systems
You ensure compatibility with newer Industry 4.0 tools and protocols by keeping systems updated. Regular patching maintains compatibility and fortifies security, a vital aspect as cyber threats grow more sophisticated. This capability requires remote access to all systems across the network, whether or not they are online. A platform such as Digi Remote Manager® has this capability, enabling rapid firmware updates for security and functionality enhancements as well as secure out of band access to any serial device for troubleshooting.
Tip 3: Leverage vendor expertise
Seek advice from vendors with proven track records in industrial IoT solutions. Digi, of course, has a wealth of experience over it's nearly four decades in providing solutions for industrial operations, and can help operations of any size to define their needs and configure and deploy secure, scalable, reliable and easy to manage solutions.
Tip 4: Test in real-world scenarios
Jerry Han, CMO at PrizeRebel, explains, "Before full-scale deployment, test your setup in real-world scenarios. This hands-on approach will quickly reveal compatibility issues, allowing for timely adjustments."
For instance, you might discover that a certain Digi XBee® 3 module works exceptionally well with a specific set of IoT sensors in your factory setup.
3. Identifying the right scenarios and applications
Implementing industry 4.0 technologies starts with pinpointing where this tech can genuinely create value. Distinguishing the appropriate scenarios and applications can make all the difference. Here's how to get it right.
- Assess real-time needs: Data processing is essential for many Industry 4.0 applications. Industries that rely on immediate data processing, like manufacturing sectors using precision robotics, can benefit immensely. Evaluating your operations to see where quick data processing could eliminate lags and enhance performance is vital.
- Determine data volume: Not all data must be stored in the cloud. Situations where sending large amounts of data to the cloud isn't efficient or economical are ideal for localized processing solutions. Tools like Digi Remote Manager® can help manage data flow, ensuring optimal distribution between local and cloud storage.
- Scalability matters: Consider your organization's growth trajectory. As your business expands, so do your computational needs. Utilizing flexible processing solutions ensures your system can scale without issues as demands increase.
- Security and compliance: Cybersecurity is more critical than ever before, especially in regulated industries and in any business where a security breach and associated business interruption poses high business risk. Solutions like Digi TrustFence® offer embedded security, ensuring that data processed at the edge remains secure. Additionally, Digi supports FIPS 140-2 compliance, which is required for any solution that is used or deployed by a U.S. or Canadian government agency.
- Review maintenance and accessibility: Deploying technologies in remote or harsh environments demands robust maintenance strategies. A minor issue can disrupt the system and the real-time data processing it supports. Moreover, the geographical spread of these technologies complicates the logistics of hands-on support.
4. Continuous monitoring and updates for maximum efficiency
Continuous monitoring is crucial in maximizing the efficiency of Industry 4.0 technologies. This is especially crucial as edge devices situated at the front lines of data collection can encounter real-world variables affecting their performance. Environmental factors, physical obstructions, or software anomalies can interrupt or degrade data streams.
Additionally, the fast-paced evolution of technology means that the software and hardware components of edge devices will regularly need updates.
Max Wesman, Founder and COO of GoodHire, states, "An outdated system runs inefficiently and can be a security risk. Implementing a robust update protocol ensures that edge devices are equipped with the latest algorithms, security patches, and performance optimizations."
But there's more than just technological housekeeping to consider. Continuous updates also mean staying updated with the latest methodologies and best practices.
As industry 4.0 technologies continue to evolve, so do the strategies for their effective deployment. By embracing a continuous learning and adaptation culture, businesses can ensure that their strategies align with the latest and most efficient practices in Industry 4.0. Digi Remote Manager, the command center for IoT and industrial IoT deployments, can provide the "single pane of glass" visibility and control to monitor and manage your deployment.
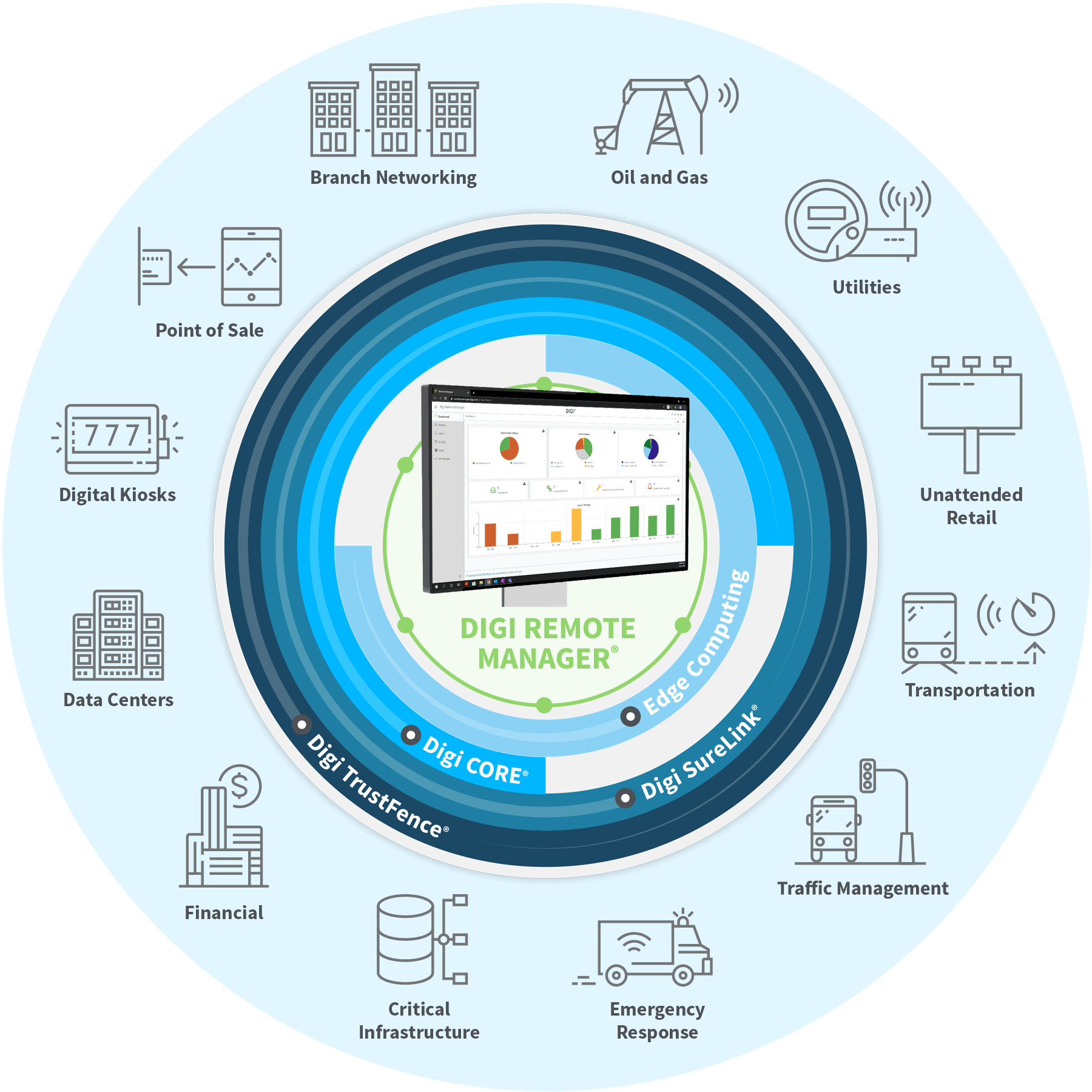
Challenges and Considerations in Adopting Industry 4.0 Technologies
Integrating New Technologies with Existing Systems
One significant challenge in the transition to Industry 4.0 is the complexity of integrating new technologies, such as advanced data analytics and IoT solutions, into existing infrastructures.
These systems, developed over the years and deeply embedded in current processes, often rely on legacy software and older data formats. Bridging this gap requires substantial effort and resources, not just for system upgrades but also for ensuring data consistency and compatibility.
Furthermore, this challenge extends beyond technical aspects. Employees accustomed to traditional systems must adapt to and be trained in these new, more advanced technological frameworks, ensuring a smooth transition into the Industry 4.0 era. That's where a team like Digi Professional Services comes in. This team of engineers has the ability to support everything from project scoping to system integration and team training to ensure your digital transformation goes smoothly.
Considerations for Initial Investment and ROI
Embracing Industry 4.0 technologies requires carefully assessing initial investments versus long-term returns. This consideration includes expenses for new hardware, software licenses, employee training, and potential infrastructure modifications.
Shawn Plummer, CEO at The Annuity Expert, emphasizes the importance of evaluating these costs against the long-term benefits. "These benefits include improved data processing speeds, operational efficiency, and potential cost savings over time. For instance, while initial investments in modernizing equipment might seem substantial, the resulting enhancements in operational processes can lead to significant long-term savings and increased productivity."
Maintenance and Technical Support in the Industry 4.0 Context
Maintaining new technology systems in Industry 4.0, especially those deployed in demanding or remote environments, requires robust strategies. Consistent maintenance is crucial to prevent disruptions in real-time data processing and overall operations.
Additionally, the rapid pace of technological advancement necessitates regular software updates and system checks to ensure optimal performance and security.
The human element is also a key consideration. As technology evolves, the need for specialized knowledge and continuous training becomes more apparent. Organizations must invest in skill development and knowledge acquisition to keep pace with technological advancements, ensuring that their teams can fully leverage the potential of Industry 4.0 technologies.
Conclusion
Are we on the brink of a new industrial epoch, shaped by the broad spectrum of Industry 4.0 technologies? As we've explored, these technologies collectively drive a significant leap in operational efficiency, innovation, and a redefinition of traditional industrial practices.
Embracing the diverse facets of Industry 4.0 is about more than keeping up — it's about leading the charge towards a technologically advanced future. The insights and tips presented in this guide equip organizations to adapt and spearhead progress in this rapidly evolving landscape.
In considering the transformative power of Industry 4.0 technologies, it's clear that we are entering a new era of industrial evolution. With guidance from pioneers in the field, like Digi, businesses can navigate this transition confidently, ready to thrive in a smarter, interconnected industrial world.
Next Steps
About the Author
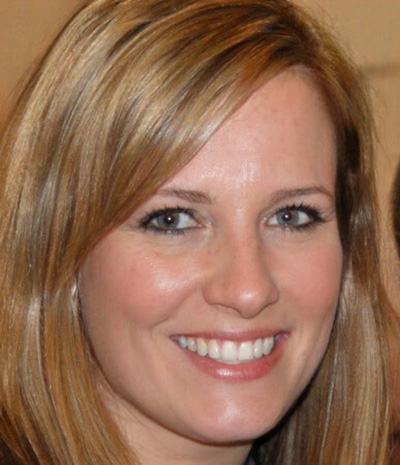
Catherine Schwartz is an author with a passion for all things digital. Her articles focus on AI, IoT, and the impact of new technologies on society.